高硬度、耐摩耗性、耐高温性を特徴とする超硬合金製丸刃は、工業加工分野における重要な消耗品となっており、需要の高い様々な業界で使用されています。以下は、業界シナリオ、加工要件、そして刃の利点の観点から分析したものです。
I. 金属加工産業:切削・成形用コアツール
- 機械製造分野
適用シナリオ: 自動車部品 (エンジンシリンダーブロック、ギアシャフト) および工作機械付属品 (ベアリングリング、モールドコア) の旋削およびフライス加工。
ブレードの利点:超硬合金製円形ブレード(CBNコーティングブレードなど)は、高速切削時の高温・高圧に耐えることができます。鋼材(45#鋼、合金鋼など)の場合、切削精度はIT6~IT7レベルに達し、表面粗さはRa≤1.6μmとなり、精密部品の加工要件を満たします。 - 航空宇宙製造
主な用途: チタン合金の着陸装置およびアルミニウム合金の胴体フレームのフライス加工。
技術要件:航空宇宙材料の多くは高強度軽合金です。円形刃には、加工中に刃と材料間の化学反応を防ぐため、TiAlNコーティングなどの耐凝着性が必要です。また、刃先円弧設計は切削振動を低減し、薄肉部品の加工安定性を確保します。
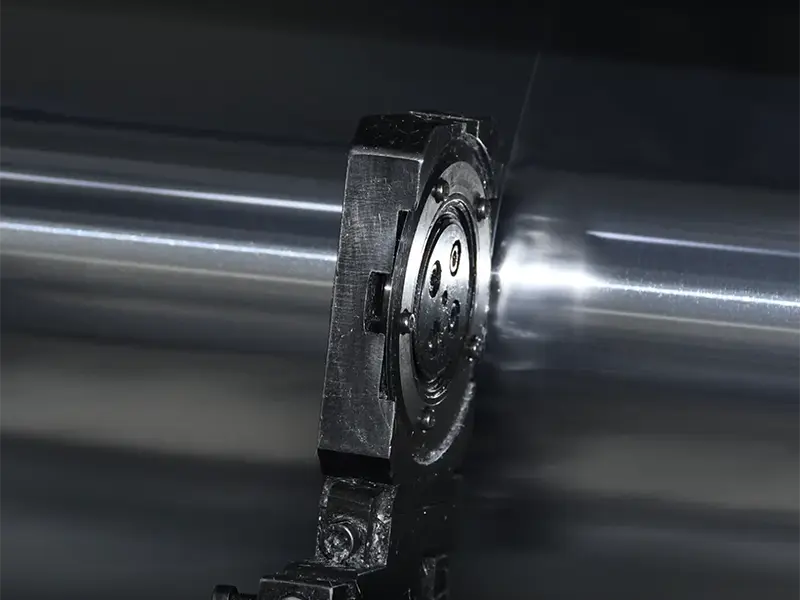
II. 木材および家具加工:効率的な切断のための標準
- 家具製造
適用シナリオ: 密度ボードおよび多層ボードの切断、および無垢材家具のほぞ継ぎ加工。
刃の種類:YG6Xなどの微粒子超硬合金製の丸鋸刃は、鋭利で耐摩耗性に優れた刃先を備えています。切断速度は100~200m/sに達し、刃1枚あたりの耐用年数は高速度鋼刃の5~8倍と長く、板材の大量生産に適しています。 - 木材フローリング加工
特殊要件:ラミネートフローリングの溝切りには、高い耐衝撃性を備えた刃が求められます。円周方向に均一な力を受ける円形刃の設計により、刃先欠けのリスクを軽減します。また、ダイヤモンドコーティングなどのコーティング技術により、切断時の摩擦熱を軽減し、板端の炭化を防止します。
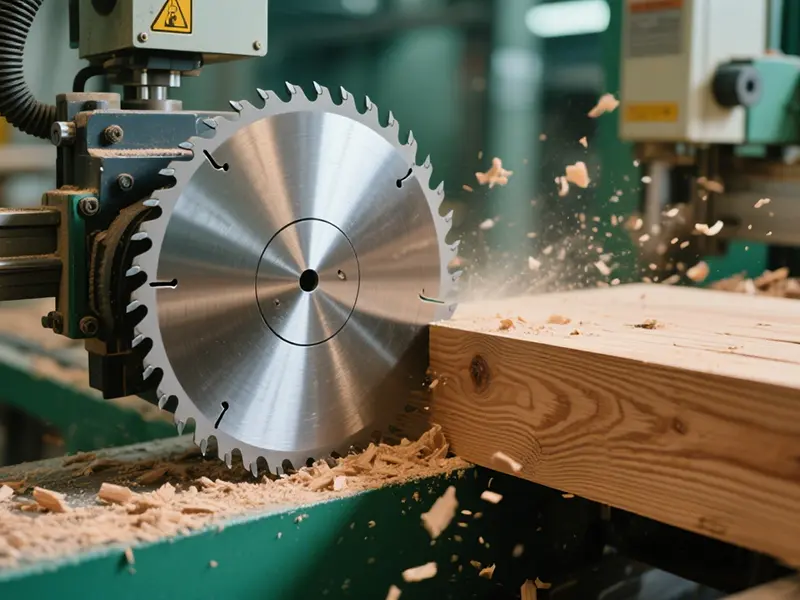
III. 石材および建築材料:硬質および脆性材料のソルバー
- 石材加工産業
適用シナリオ: 花崗岩や大理石の原石の切断、セラミックタイルの面取り加工。
ブレード特性: WC-Co セメントカーバイドマトリックスと多結晶ダイヤモンド成形体 (PDC) を組み合わせた円形ブレードは、HRA90 以上の硬度を持ち、モース硬度 7 未満の石を切断でき、切断効率は従来のシリコンカーバイド研削ホイールよりも 30% 高くなります。 - 建設工学
代表的な事例: コンクリートプレハブ部品(橋梁鉄筋コンクリート部品など)の穴あけおよび溝入れ。
技術的ハイライト:円形刃の水冷構造設計により、切断熱を適時に逃がし、高温によるコンクリートのひび割れを防止します。また、鋸歯状の刃先設計により、脆性材料の破砕能力が向上し、粉塵汚染を軽減します。
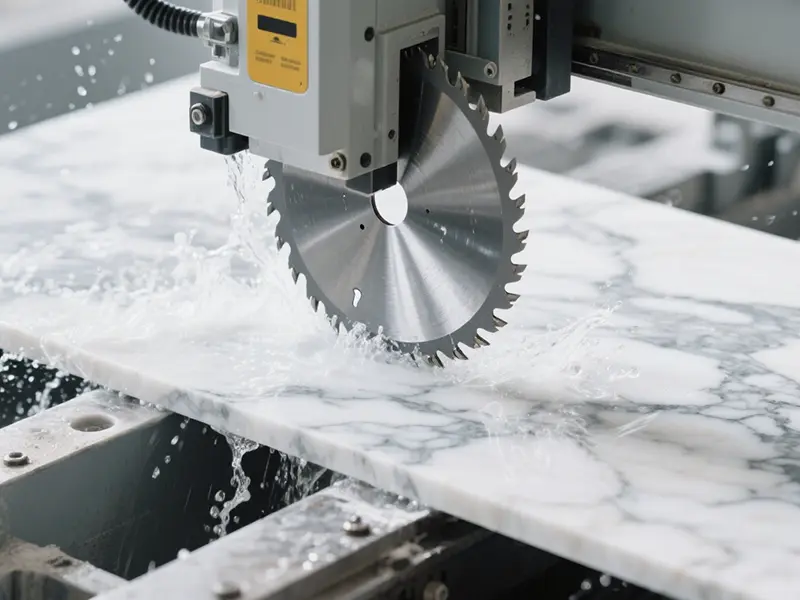
IV. エレクトロニクスと精密製造:ミクロンレベルの加工の鍵
- 半導体パッケージング
適用シナリオ: シリコン ウェーハの切断、PCB 回路基板のデパネル化。
ブレード精度:超薄型超硬合金製円形ブレード(厚さ0.1~0.3mm)と高精度スピンドルを組み合わせることで、シリコンウェーハ切断時のチッピング量を5μm以内に制御し、チップパッケージングにおけるミクロンレベルの加工要件を満たします。さらに、ブレードの高い耐摩耗性により、バッチ切断時の寸法安定性を確保します。 - 精密部品加工
主な用途: 時計のムーブメントギアや医療機器用の低侵襲手術器具のフライス加工。
利点:円形刃の刃先は鏡面研磨(粗さRa≤0.01μm)されているため、加工後の部品表面の二次研磨は不要です。また、超硬合金の高い剛性により、小型部品の加工中に生じる変形を抑制します。
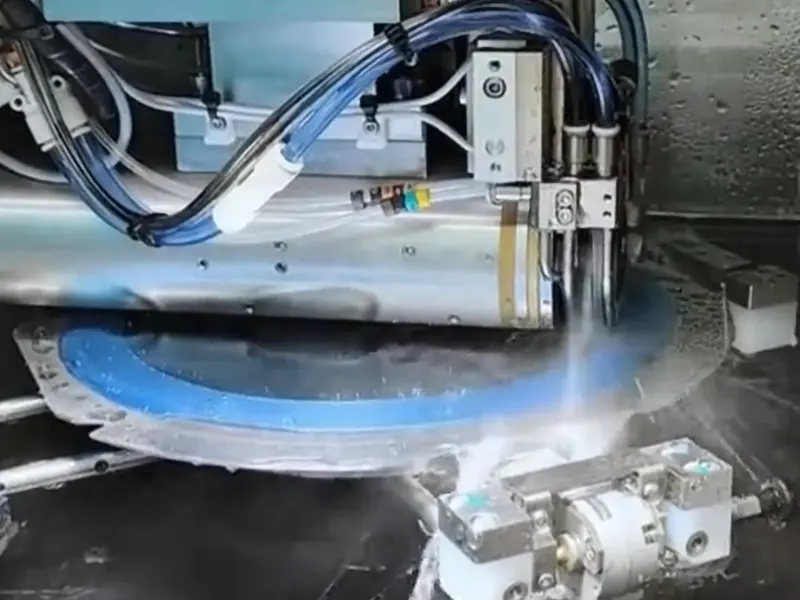
V. プラスチックおよびゴム加工:効率的な成形の保証
- プラスチックフィルム製造
適用シナリオ: BOPP フィルムのスリット加工、プラスチックシートのトリミング。
ブレード設計:円形スリットブレードは、プラスチックがブレードに付着する現象を軽減するために、負のレーキ角を持つ刃先設計を採用しています。定温制御システムと組み合わせることで、150~200℃の加工温度でも鋭い刃先を維持し、スリット速度は500~1000m/分に達します。 - ゴム製品加工
主な用途: タイヤのトレッドの切断、シールの打ち抜き。
技術的利点:超硬合金円形ブランキングブレードの刃先硬度はHRC75~80に達し、ニトリルゴムなどの弾性材料を50,000~100,000回繰り返しブランキングでき、刃先の摩耗量は0.01mm以下で、製品の寸法の一貫性を保証します。
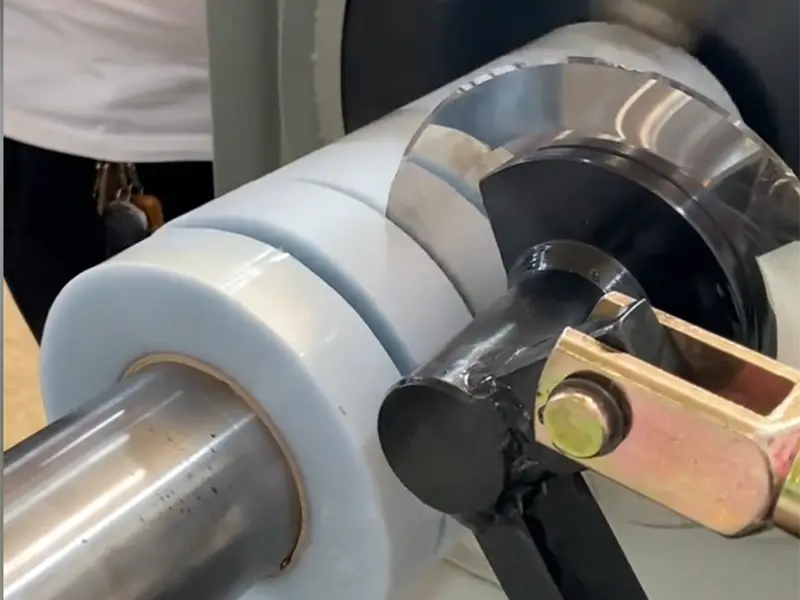
投稿日時: 2025年6月17日